by
[user not found]
| Jun 23, 2014
I say "Gemba", you say, "What?"
"Gemba!"
"What?"
"Gemba!"
"What?"
Gemba is a word that is unknown to the vast majority of Americans. Unless you're among Lean folks, mention the word and you're going to be met with a blank stare or a confused look.
Fundamentally speaking, the Gemba is the place that matters most. It's the place where value is created for the customer and it's the heart of any business. For some it's the sales department, for others it's the delivery team. For many companies that embrace Lean management and manufacturing's best practice and philosophies, the Gemba is the factory floor.
This past week, a small team of VIBCO employees from production and sales area had a chance to participate in a Gemba Walk - a personal observation of work where the work actually happens through unbiased eyes - at Gemline Corporation in Lawrence, Massachusetts.
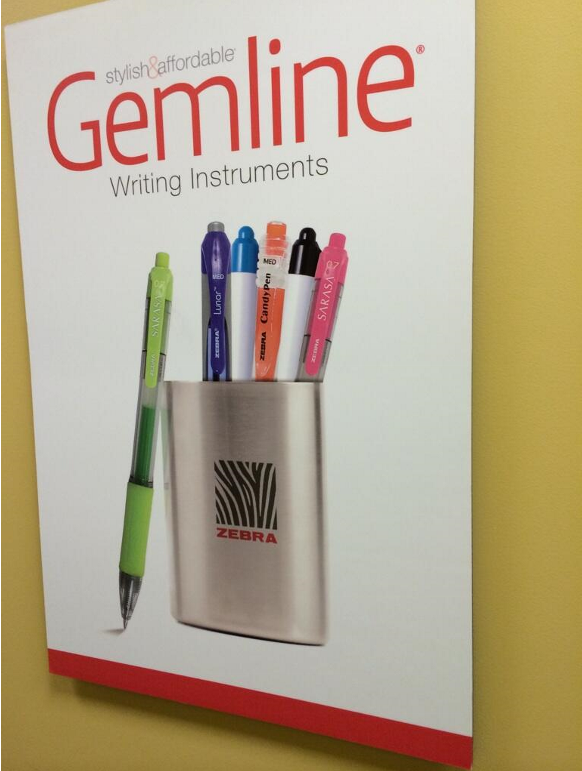
The Gemba walk isn't just a guided promotional tour through a factory. No window dressing, no hiding problems - it's a real look at the real work being done. It is not about showing off the highlights of the factory or reciting this quarter's and this year's achievements and accomplishments, nor is it a time to find fault in others while they're being observed.
Gemba is all about ideas.
A Gemba walk is where direct observation is an improvement idea bonanza. It means to actually go to the Gemba location and see where and how the work is happening. A Gemba walk focuses on:
- Observation: in person observation or actually going out and seeing the Gemba for yourself
- Value: Seeing where the work is being done as opposed to discussing a warehouse problem in a conference room
- Teaming or interacting with the people and process in the spirit of Kaizen or "change for the better"
Gemba walks are active learning experiences where each person on the walk is encouraged to ask questions, and wonder why things are happening the way they are… all with the specific goal of learning, and developing ideas for change and continuous improvement.
The VIBCO's teams Gemba at Gemline put the power of Ideas into sharp perspective.
Ideas are Free
Before we visited Gemline's factory floor, we visited Gemline's business floor. The business floor is on the 2nd story and is the main location for Gemline sales, marketing and design. As we walked in, we saw loads of tables with Gemline representatives sharing their company's achievements with other people interested in seeing and learning from them.
Each division of Gemline had a table. There was the marketing table, the IT table, the human resources table, accounts receivable, continuous improvement and many other sections - each with their own decorated tri-fold presentation board full of charts, tables, pictures and visuals highlighting their divisions accomplishments and achievements. Gemline team members were proud to share how much they had improved from year to year, but they became kids on Christmas morning when talking about how ideas are transforming their company.
Every single department shared how ideas and an ideation culture is accelerating the growth of their company (ten-fold!!!) and introducing unimaginable levels of improvement. Moreover, every Gemline division had a high level of idea success and implementation - over 70% for each division!
"How the heck is Gemline doing it?" we wondered.
The answer? Idea Boards, Leadership Commitment to Operator-Led Idea Implementation, and Discipline.
Idea Boards are large bulletin boards placed in each department. Employees with ideas write down the idea and tack it to their board. Every week, each department gets together, discusses the ideas on the board and determines a plan of action. They do this based on a number of parameters including urgency, do-ability and impact.
According to just about everyone we talked to at Gemline, Ideas are the reason they are successful. Ideas replace legacy systems with modern ones. Ideas unify their factory workforce and create a culture that is empowered to enact change. Ideas are shaping the future of Gemline.
For the VIBCO team, the notion of Ideas resonated… big time. Our pencils couldn't scribble notes down fast enough and we all took a ton of pictures. At Gemline, Ideas aren't dying by committee, they aren't hiding behind job titles and responsibilities. They are out in the open for all to see and get involved in implementation. The passion at Gemline is clear. We could feel their belief in the power of ideas and we were incredibly impressed with their systematic, democratic and transparent process to impact the company's direction, mission and goals.
The Walk
After the office floor "show and tell", we headed down to the factory floor for a tour of Gemline's production operations.
The sheer size and scale of the factory was staggering. The factory extended far out in all directions with stations and machinery aligned to promote the flow and movement of product and raw material throughout the plant. Each station features visual aids to support standard work.
We saw Gemline production lines, we reviewed samples from recently completed orders, and we observed different signals and systems that have been developed over the years to help solve problems and reduce waste.
Then our host took us over to the factory floor's idea board. Their idea board was similar to those we had seen in the marketing and IT department. A long white board chuck full of Ideas Cards with suggestion and input from workers all around the factory!
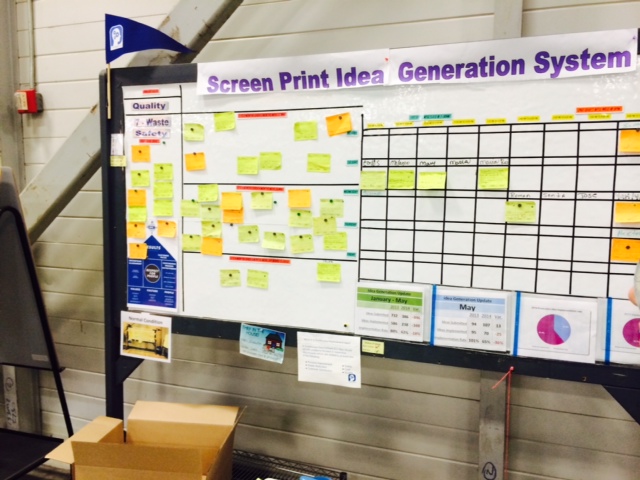
Here's how the board works:
- Someone has an idea.
- They write the idea on an orange idea card and put it on the board.
- Every Monday, the factory team gets together and reviews the submitted ideas.
- The team votes on the priority and discusses how the ideas can be implemented.
- Ideas that don't have a high priority still remain on the board for later votes.
- All ideas are reviewed and all ideas get attention.
The ideas that get top priority go to the top of the board. At that point, a team member volunteers to work on the idea. They block a section of time out of that week's work schedule and are expected to report back on progress the following week.
If an idea hasn't been implemented within two months, it moves down the board to another quadrant. It doesn't disappear. It's just set aside into another section of the board denoting that this idea is older than 2 months. It's still free for anyone to pick up and work on.
What about the ideas that no one volunteers to implement? They stay on the board for 6 months and then either drop off or are elevated for additional resources and support.
To us, the system seemed fluid, self-regulating and the results spoke for themselves.
It is clear that, at Gemline, Ideas are a primary driver and goal for every single employee. Leadership has provided a structure to capture ideas, managers have standard work to review ideas, and operators have standard work to IMPLEMENT ideas. The system works.
What We Learned
After returning to VIBCO the next day, our team of five shared what we learned from the Gemline Gemba walk.
We shared our excitement about Gemline's Idea Boards with our VIBCO team members. VIBCO has tried a few different approaches to Ideas… with some good success as evidenced by the massive number of operator-led improvements all over VIBCO. But what we haven't done well is to provide a concrete structure to those ideas with standard work for the review and implementation process.
Our visit to Gemline provided inspiration and a template… now we have to go put it to work!
UPDATE! As of last week, we finally put together our first Idea Board here at VIBCO and within minutes, it was already being populated with ideas!
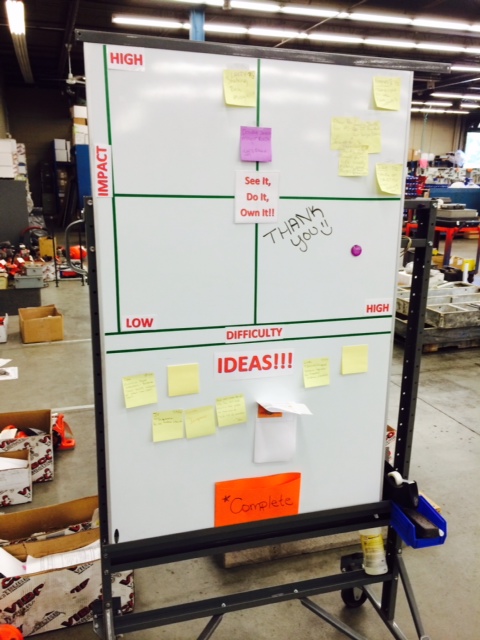
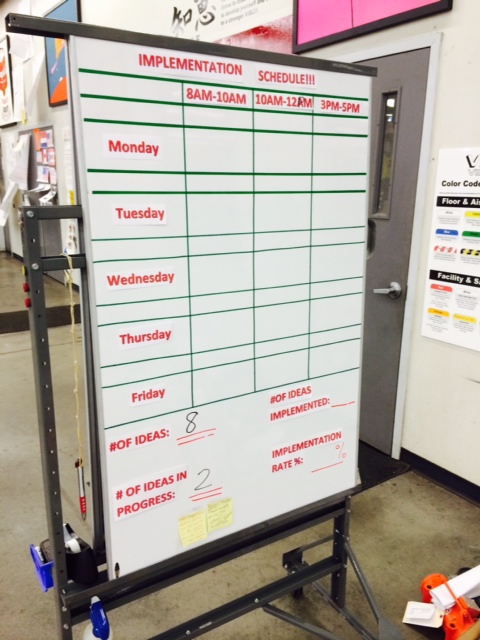